Loom Spotlight: Backstrap Looms
equipmentBackstrap looms are one of the simplest designs of loom used for weaving long fabrics, where the tension is held between the weaver's back and some other point. However, being simple to make doesn't mean they only make simple fabrics!
You can use a wide range of things as an anchor - a tree branch or fence post outdoors, or a clamp, a sturdy piece of furniture indoors, or a door knob indoors, or even the weaver's feet. Backstrap weavers can get very creative at finding anchors! If using a door knob make sure no one will open the door while you're weaving!
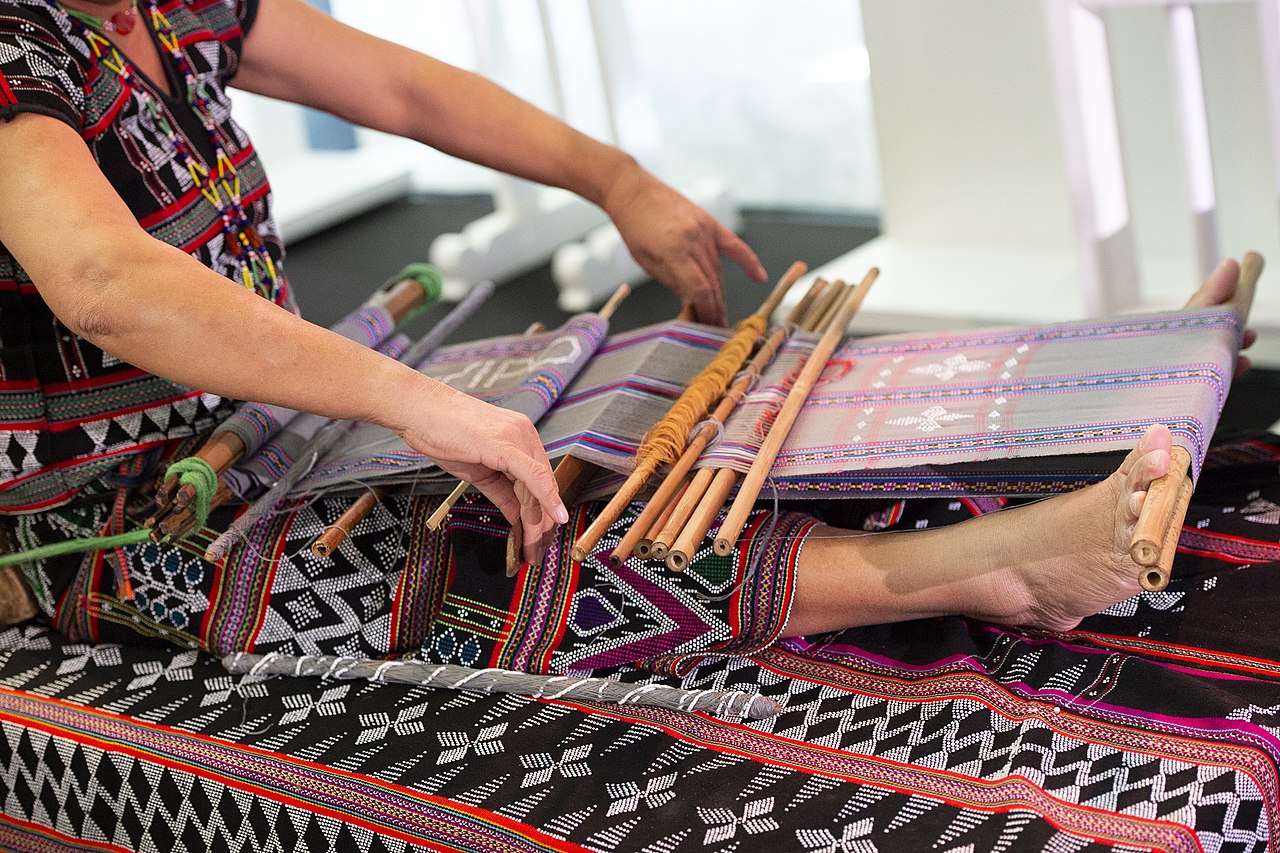
By Violaine Martin CC BY-SA 4.0, Link
The term backstrap loom covers a variety of designs that have been used traditionally in Asia and the Americas, particularly Central America and the Andes - there's many different variations in style and technique that exist in terms of loom design and weaving techniques. Backstrap style weaving has also existed in other areas for narrow bands only, such as Sámi band weaving in northern Scandinavia. There are other styles of simple looms like warp weighted looms and horizontal ground looms that were used historically in other areas.
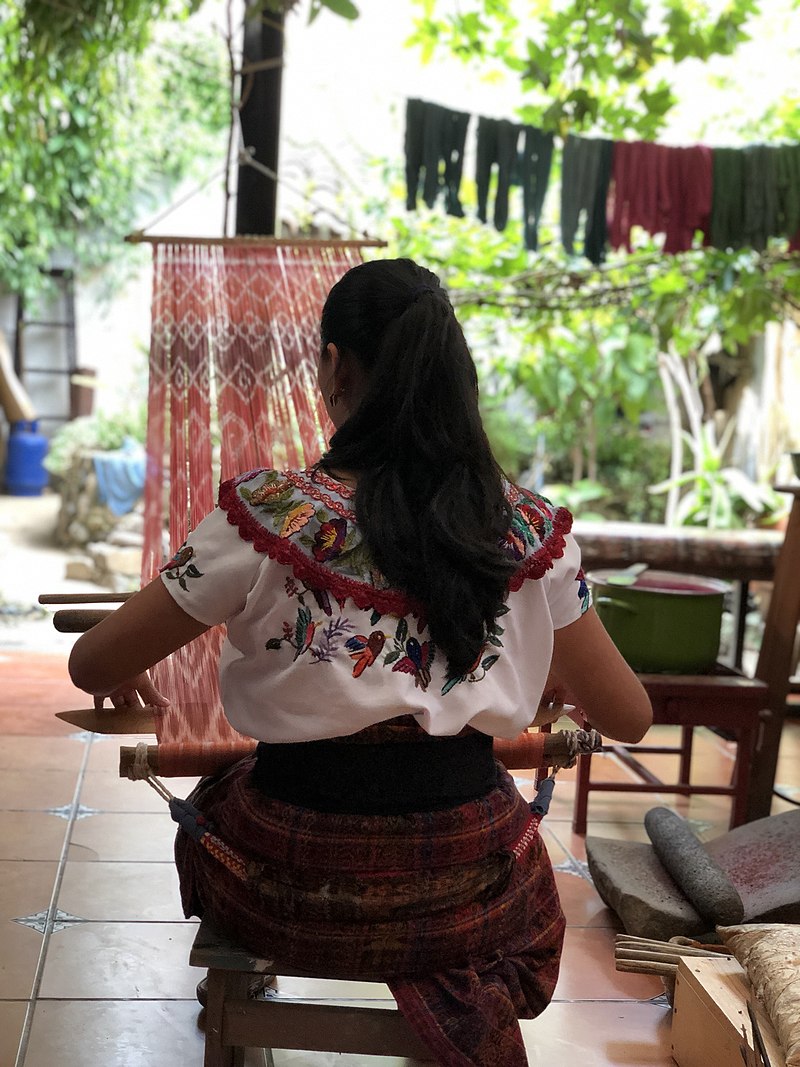
CC BY-SA 4.0, Link
For weaving narrow bands, all you need is an anchor point and something to attach it to the anchor and a belt or sturdy cord. At it's simplest this can just be some knotted cord, but plastic clips or wooden bandlocks can also be used to make it easier to advance. Narrow bands are often woven using small rigid heddles, which can have multiple sets of holes or sizes of slots to facilitate certain types of pick-up patterning. Stoorstalka is one maker of this style of heddle, but there are many other small sellers. Rigid heddles used in this way have a substantial amount of draw in and are not used to beat. Bands can also be woven using string heddles or tablets to make the sheds.
For wider warps, you need some sticks or dowels to spread the warp for more even tension, and the backstrap piece is wider than a belt and attached to a bar for your fabric. Most often string heddles are used, which typically makes warp faced fabric (more balanced fabric is possible, but difficult), though a rigid heddle such as one from a rigid heddle loom can be used to make a more balanced fabric. Most backstrap weaving tends to be not much wider than the weaver, e.g. about 2 feet or less, but some expert weavers use wider warps, I have seen reports of 39" or more.

Adrian Dascal via Unsplash
People often DIY their backstrap looms with dowels from a hardware store however there are smaller sellers selling backstrap kits. Backstrap weavers typically use a stick shuttle and may use a shuttle with a beveled edge or a sword to beat depending on style.
Pros and Cons of Backstrap Looms compared to Rigid Heddle Looms #
A backstrap loom is extremely low cost; at it's simplest it can be made with found materials, and even pre-warped starter kits are around 1/3 the cost of a small rigid heddle loom. Backstrap looms also take up very little space when stored - some yarn rolled up around some dowels.
However it may be harder to find a spot to do your backstrap weaving with a suitable anchor and enough space, and it's harder to quickly start and stop your weaving. I often do a few picks at a time on my rigid heddle loom in between steps of making dinner, for example, which wouldn't be practical with backstrap style weaving. There's more of an opportunity to turn a project into a tangled mess of yarn if it's not put away correctly.
Backstrap looms with string heddles excel at making warp faced fabric of a kind that can't really be done on a rigid heddle loom beyond narrow bands. For making a more balanced fabric with a backstrap technique, you can use a rigid heddle from a rigid heddle loom, so if you do get into both styles of weaving there's overlap in tools.
In the initial learning process, there's more that can go wrong than with a rigid heddle loom. It's highly recommended to start with a warp made by an experienced weaver, either as a kit such as the ones by Kakaw Designs or a local teacher, or else start with very short and narrow warps and slowly work up over several small projects, as it's very difficult to weave on a poorly prepared warp. While I certainly advocate starting small with a rigid heddle loom, my first project was a 10" wide scarf, while with backstrap weaving small might mean a 1" wide band on a 1 yard warp with several projects to work up to progressively wider and longer fabric.
Both rigid heddle looms and backstrap looms are best at producing not too wide fabric, up to around 24". A rigid heddle loom is easier to go somewhat wider than that, but a floor loom is the best option for going beyond 32".
There's very little downside to trying out backstrap weaving, as the cost is minimal especially for band weaving where you don't even need to spread the warp and can simply tie on to a belt. And learning how to weave narrow warp faced bands backstrap style can make a great complement to your rigid heddle weaving projects, and with wider backstrap weaving you can produce a different range of fabrics than you can on a rigid heddle loom.
Check out Not So Rigid Designer, the online weaving software for rigid heddle loom weavers!
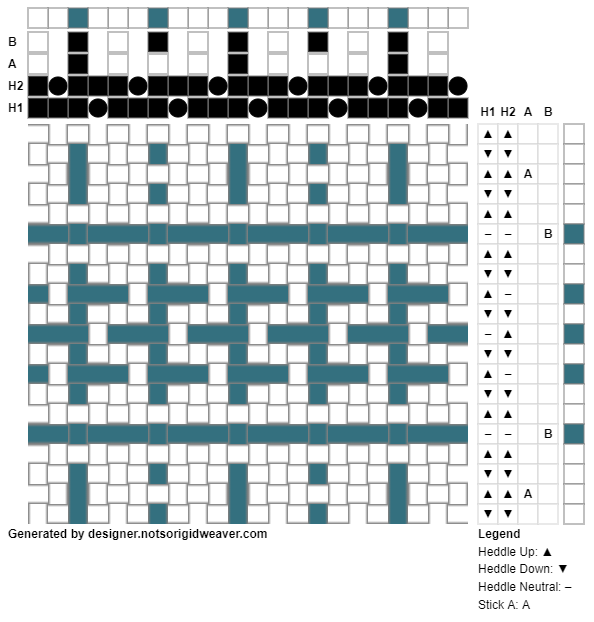