So what can’t a rigid heddle loom do?
loomRigid heddle looms are great little looms and I love them, but no loom is the right tool for every job, and there are some things that rigid heddle looms really fundamentally can’t do. This post will dive into those!
A lot of this comes down to sett, so I’ll define a couple related terms that I’m going to use:
- Dents Per Inch (DPI): How many holes and slots there are per inch in the heddle or reed.
- Ends Per Inch (EPI): How many warp ends there are per inch in the fabric. EPI and DPI are equal if there is one thread in each ‘dent’ (aka hole or slot)
- Sett: How many EPI there are.
- Density: The ratio of DPI to EPI. 100% density is 1 end per dent. 200% density is 2 ends per dent. This is affected by doubling yarns, using multiple heddles, and using fancier structures, for example a point twill might end up at 150% or 75%. For more detail on density and structure, check out Liz Gipson’s post on Threading Part Two: Sett In A Multi-Heddle World.
Now onto the things rigid heddle looms can't do!
Precise control over sett #
On shaft looms, the reed and heddles are separate, and it’s very common to thread multiple yarns per slot in the reed. With just one reed you can usually sett things to within about 3EPI and with access to a couple different reed sizes you can usually get to within 2 EPI or less. But on a rigid heddle loom, your structure and sett are tied together, there’s fewer options of reed sizes, and particularly in the double heddle range you can have options that are more like 5 EPI apart.
This matters most when you really want a balanced weave, like a pattern that needs to be square, that also isn’t too loose or too stiff! This also makes rigid heddle looms less flexible for ‘crammed and spaced’ effects. Variable dent heddles help with this, but still limit your options somewhat. Many fabrics aren't perfectly balanced though!
The advantage of this is that there’s fewer options to sample given a particular yarn, and the differences between them will be bigger, so if you’re the sort to obsess over details, you don’t need to spend time deciding if 18, 20, or 22 EPI is best because you can only do 20 EPI!
Really fine fabric #
Rigid heddle looms are best suited for thicker fabric. The finest rigid heddle on the market is Ashford’s 15 DPI and many other brands go down to 12 - there’s only so fine they can be made and still be strong enough, and the hole and slot design necessitates thicker material than a metal reed for a shaft loom.
There are lots of ways to go below 15 EPI in the fabric, using double and triple heddle techniques, doubling (or more!) yarns in each slot and hole, and combining the two together, but, to weave a structure using single yarns, you’re mostly limited to 200% density (so up to 30 EPI) or if you’re working with smooth yarns and have a lot of patience to deal with not very clean sheds you may be able to pull of 300% with triple heddles, which could conceivably take you to 45 EPI; this is definitely pushing the limits and I haven't really seen 300% density in the wild.
This range is thick compared to most commercial fabric, but a great deal of handweaving is in the range achievable with 2 heddles - flipping through a couple issues of Handwoven, which focuses on floor and table loom weaving, their most common setts are 20 and 24, with a project or two being lower than that and a few projects being higher.
This doesn’t mean that you can’t weave with fine yarns though! As an extreme example, the ‘Spider Silk Shawl’ project in Inventive Weaving on a Little Loom uses a very fine silk yarn using 6 strands and double heddle techniques. While the end result is lovely and takes advantage of multiple strands for some interesting color blending, it is a very different fabric from weaving the same silk as a plain weave structure, and in many ways more like working with thicker yarns to begin with.
Wide warp faced weaves #
Warp faced weaves are those where the warp ends up completely covering the weft (except at the edges). This requires a tight sett. Rigid heddle looms can make narrow warp faced bands, and in fact historically that’s been a common use of the rigid heddle concept. In this case, you don’t use the heddle to beat and expect a lot of draw in. But wider warped faced weaves don’t work well with a rigid heddle as the rigid heddle is “chunkier” than a reed of the same DPI.
However, I think it would be possible to use backstrap style techniques like string heddles and a weaving sword (or shuttle!) to beat, but using the frame of a rigid heddle loom for tension. I haven't tried it yet, I have more ideas of things to weave than time to weave them! I debated including this on my ‘can't’ list, but with this setup it's not really being used as a rigid heddle loom!
Very long fabric #
Rigid heddle looms are not usually designed to take on huge warps. There’s not really a precise number here as it’s more about the thickness of the fabric on the roller, but think 4-5 yards or so - less if it’s thicker, maybe a little more on the very fine end. The Leclerc Bergere may take a longer warp than most as I believe it uses a table loom frame; and the Ashford Freedom Roller attachment for their Rigid Heddle line can also extend the warp length. Unlike the points about sett, this one is more about the design of available looms rather than a fundamental limitation of the rigid heddle design - rigid heddle looms are mostly fairly compact but holding a huge warp requires a bigger loom.
There are other things that other styles of loom are better at, but can be done on a rigid heddle loom with difficulty. There are also some people who get creative with modifying their rigid heddle looms and making them work as simple shaft looms, or the Cricket Quartet attachment which truly turns it into a small 4 shaft loom - but the things above really can’t be done using a standard rigid heddle loom!
Check out Not So Rigid Designer, the online weaving software for rigid heddle loom weavers!
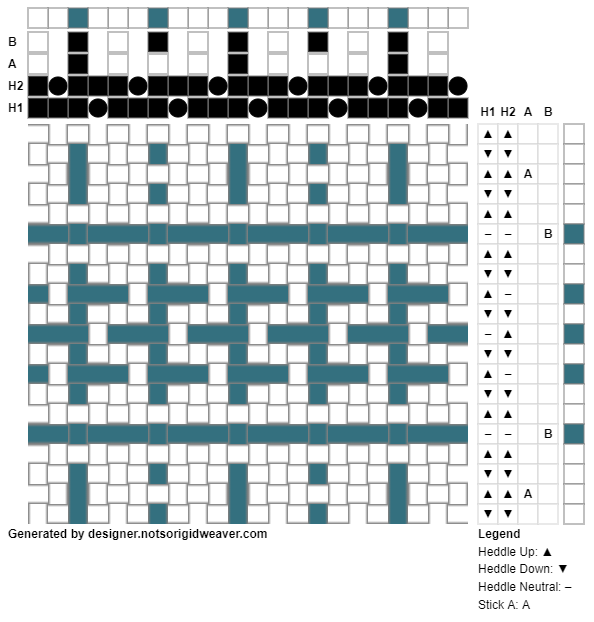