Designing a Project using Not So Rigid Designer
planning projectsNot So Rigid DesignerWeaving Softwarepick-updraftsNot So Rigid Designer is the online weaving software I’ve been building. It lets you make designs in terms of heddles and pick up sticks, rather than doing the mental gymnastics to convert from shafts - I’ve been doing those gymnastics on hard mode for you! So far as I am aware it’s the only software designed specifically for rigid heddle weavers.
I figured it was past time to show an example of creating and weaving a design using this tool!
I have multiple partial cones of a gorgeous copper silk that a friend gave to me (she’d gotten it at a stash sale and had come to the conclusion she was never going to knit anything with it!). I’ve been trying to figure out what to weave with it for a while - it’s not a color I love in large quantities, but lovely as an accent. More recently, I came across some light blue and charcoal yarn at a guild event, and realized that these would work well with the copper. I’m not sure of exact fiber composition but it seems like a wool blend of some kind. All of it is around a fingering weight, so great for a rigid heddle loom! In this case, I had tons of the copper, a decently full cone of charcoal, and a smaller amount of the blue.
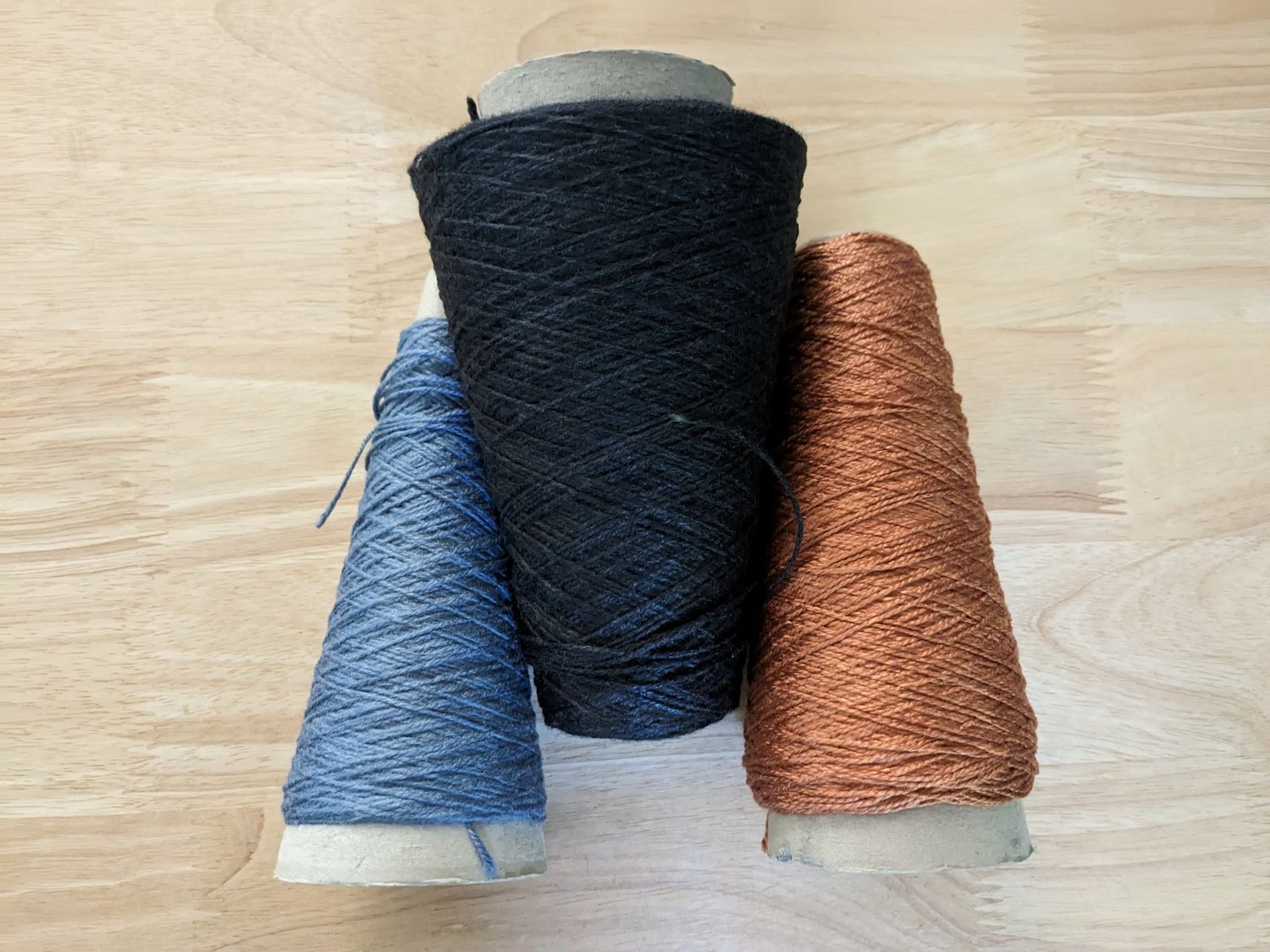
First off, I was really uncertain about the sett, so I made a sample, I played around with some options in Not So Rigid Designer and warped up something like this:
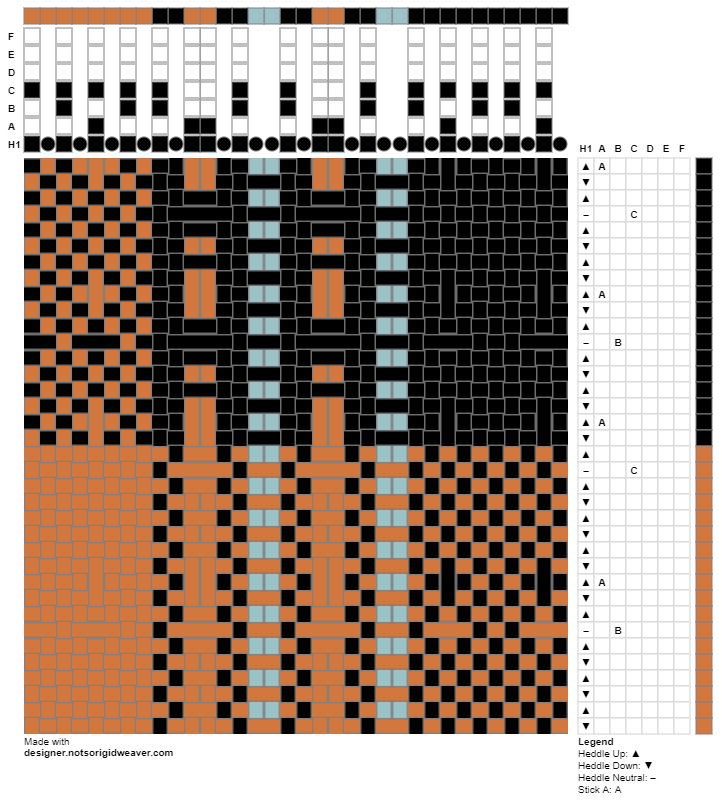
The questions I wanted to answer with this sample included things like what sett do I want to use, what kind of warp pattern do I like, what weft should I use, and how can I incorporate a fairly small quantity of blue and have an impact. I warped this up in a 12.5 DPI heddle - I thought it might be too loose, but I wanted to try it because it’s the smallest I have on my 24” loom and preferred to use it rather than double heddle if I could. Of course once I got the sample on, I went to town and tried out a bunch of different weft options. It’s not pretty, but, it’s purpose is to try out some different ideas using a small amount of yarn, and get some idea of things like shrinkage.
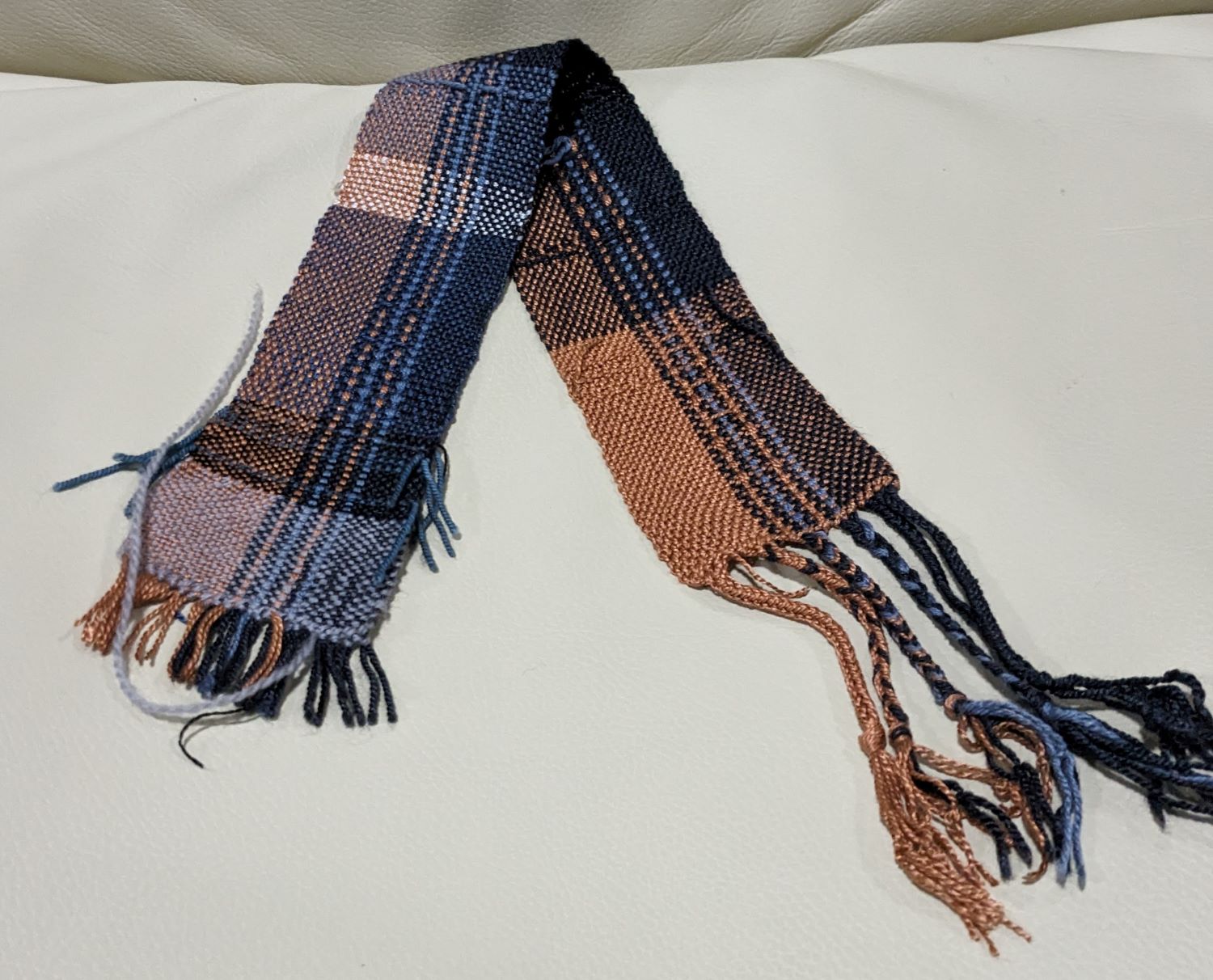
The sample told me that the sett was fine, and that I really liked the doubled stripes of blue and copper with the charcoal weft. I also liked the simplicity of just warp floats in the copper. I tried out some fingerloop braids on the fringe - I think the 5 loop square braids are a bit fat with this thickness of yarn, though the one on the right which was a 5 loop split braid is a good size.
So then I went back to the designer and played around with some options. I was a bit worried about how much blue I had and came up with a design that used fewer blue stripes as an option as well.
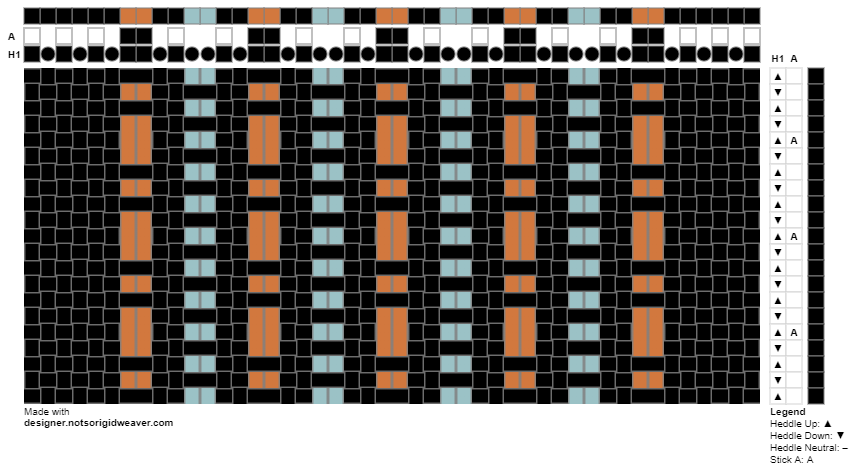
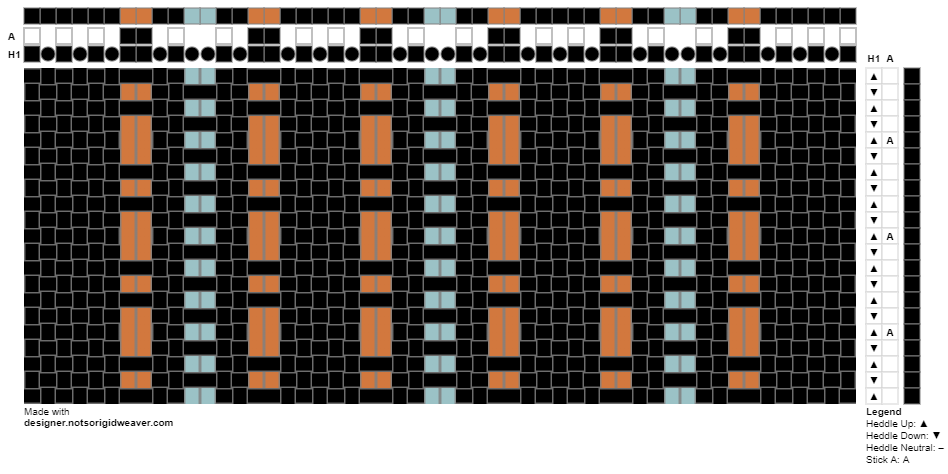
There was a bunch of back and forth on estimating how much blue and black I had using various methods to try and decide between these designs! I decided I had enough for the alternating copper and blue version. But then I messed up my calculations and had to recalculate in a panic after getting partway through warping to see if I still had enough. One thing that was helpful there was that I’d weighted the cone before starting, so I knew how much weight I had used doing 10 repeats, so I was able to confidently work out that I had enough yarn to do the total number of repeats.
When warping, I carried the black along, and tied off the copper and blue every time. I direct warped as normal except that every 3rd hole got a loop of blue. I did make sure to double check frequently and caught a few mistakes before they got too hard to deal with! While threading, I then just had to move black ones around to the nearest empty hole (which meant sometimes it was right and sometimes it was left).
In the end, I warped up the pattern about as wide as I could based on my biggest pick up stick, which is about 21” without the pointed part (I’m going to need to buy myself a 25” pick up stick so I can do full width!). Because I was pushing the stick to it’s limits, I put a cardboard warp separator in to save the pick up pattern in case the stick slips.
I’m now partway through weaving and it’s absolutely gorgeous! The overall final sett is mostly 16.6 EPI as it’s at 133% density through most of the warp. I think my shawl is coming out a little bit more warp dominant than the sample because I had the stripes throughout rather than a small accent in the sample, but it definitely was on the loose side at 12.5.
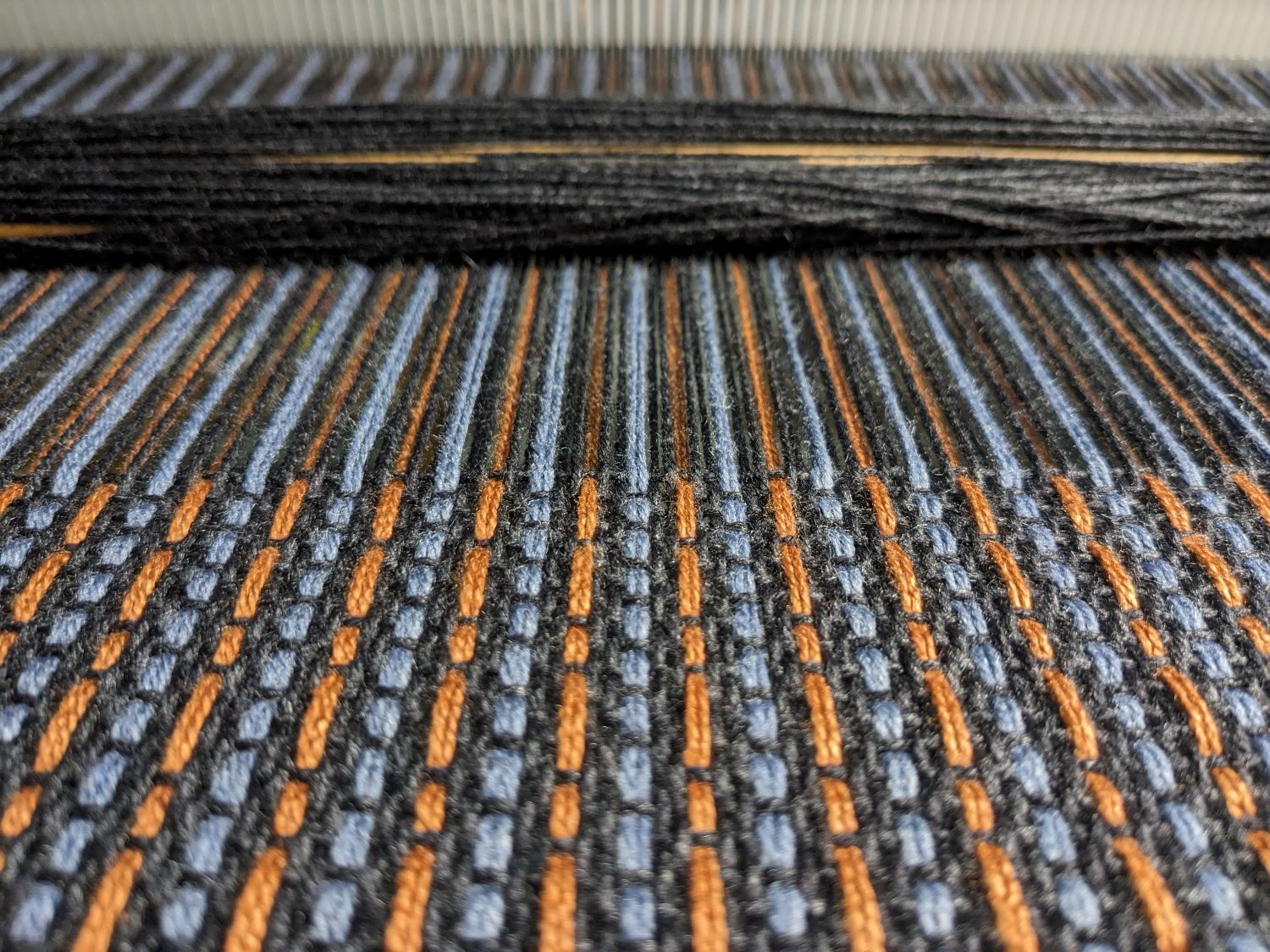
Using Not So Rigid Designer helped me iterate on some ideas faster than sampling, but since I was working with unknown yarns a sample was still important! It’s still early in it’s life, with lots more to come! Give the free demo a try!!
- Next: Ravelry for Weavers
- Previous: History of the Rigid Heddle Loom
Check out Not So Rigid Designer, the online weaving software for rigid heddle loom weavers!
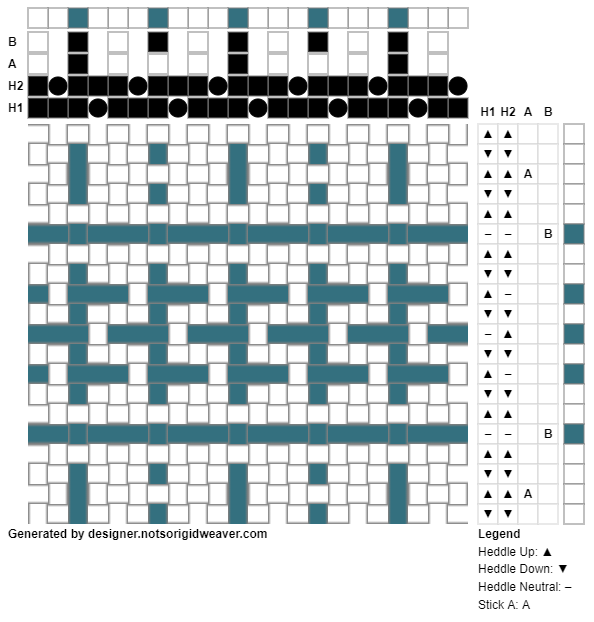